Understanding the Importance of 3 Way Manifold Valve in Industrial Applications
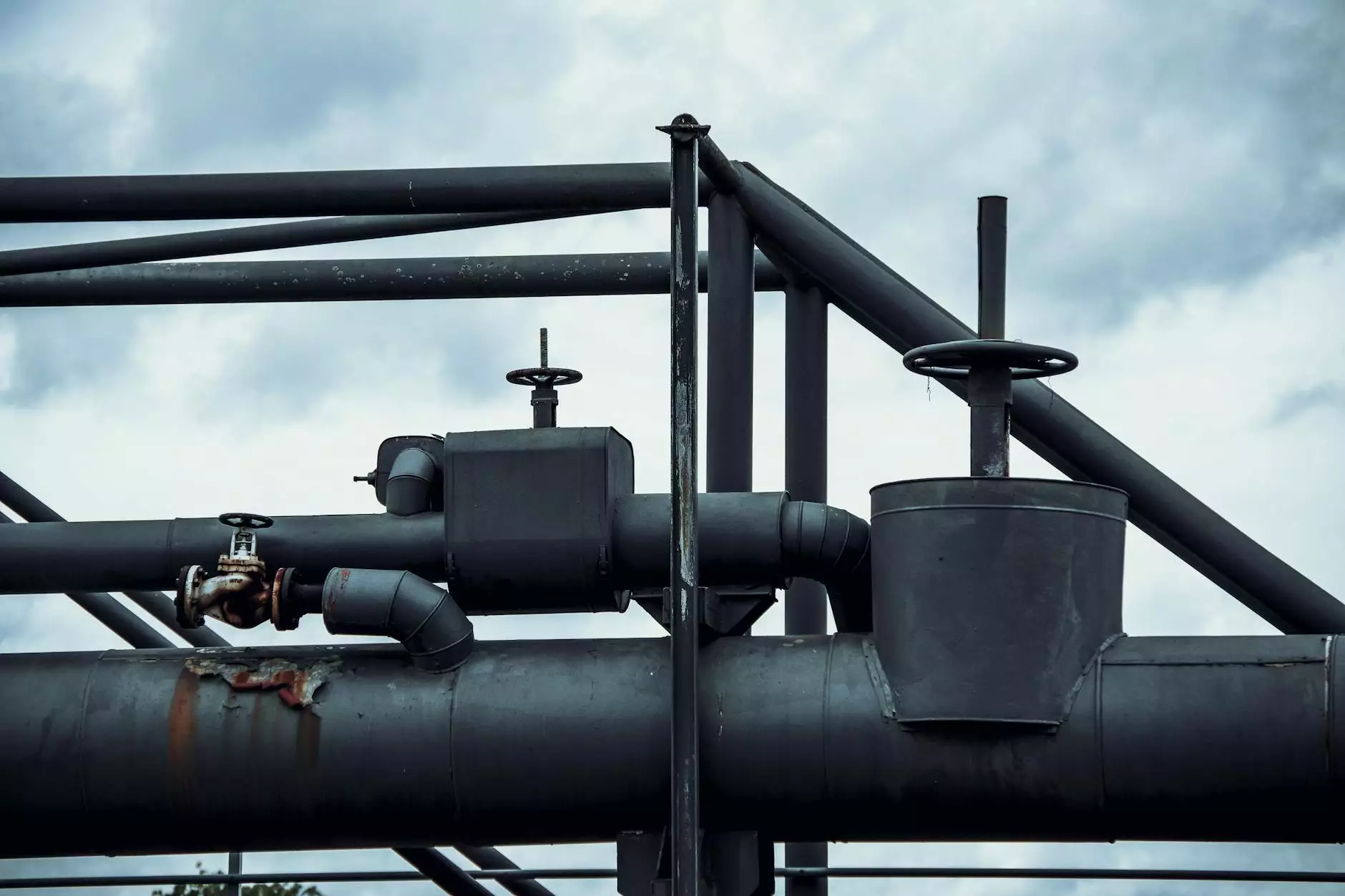
The 3 way manifold valve is an essential component in various industrial applications. Its unique design allows for a versatile operational framework, facilitating the effective control of fluids in multiple directions. As industries evolve, the demand for such efficient, reliable equipment grows, making a thorough understanding of manifold valves crucial for engineers and technicians alike.
What is a 3 Way Manifold Valve?
A 3 way manifold valve consists of three ports, enabling it to control fluid flow from one source to two different outputs or to mix fluids from two sources into one output. This design is particularly advantageous in applications requiring precise flow management, such as in chemical processing, oil and gas industries, and various hydraulic systems.
Key Features of 3 Way Manifold Valves
- Versatility: Capable of directing flow in multiple pathways.
- Precision: Allows for accurate control over fluid movement.
- Durability: Made from robust materials that withstand high pressures and temperatures.
- Compact Design: Saves space while maintaining efficiency in fluid management.
Types of 3 Way Manifold Valves
When it comes to 3 way manifold valves, they typically fall into several categories based on design and function:
1. L-Port Manifold Valves
L-port manifold valves enable flow in a straight-line connection or a right-angle path, effectively managing fluids in processes requiring directional change.
2. T-Port Manifold Valves
T-port valves offer a three-way control, allowing for more complex flow management, often used in mixing applications where two different fluid streams combine into one output.
3. Manual vs. Automatic Operation
Depending on the operational requirements, 3 way manifold valves can be operated manually through levers or knobs, or automatically via actuator systems, enhancing efficiency in high-demand environments.
Applications of 3 Way Manifold Valves
The adaptability of 3 way manifold valves makes them suitable for various sectors:
- Oil and Gas: Used for wellhead control, allowing for efficient choke management and pressure regulation.
- Chemical Processing: Essential in the handling of hazardous fluids where precise control is necessary to prevent spills and maintain safety.
- Water Treatment Plants: Helpful in redirecting and mixing different water sources and chemicals efficiently.
- Pharmaceuticals: Used in processes requiring strict control standards to maintain product integrity.
The Importance of Choosing the Right Manifold Valve
Selecting the appropriate 3 way manifold valve is crucial to optimizing system performance and ensuring safety. Factors to consider include:
1. Fluid Compatibility
Understanding the chemical properties of the fluids that the valve will handle is vital. Some materials may corrode or degrade in the presence of certain fluids, leading to system failures.
2. Pressure and Temperature Ratings
Valves need to be rated for the maximum temperatures and pressures they will encounter in service. Insufficient ratings can lead to catastrophic failures.
3. Maintenance Requirements
Regular maintenance is necessary to ensure the longevity of the valves. Choose designs that allow for easy access and servicing to reduce downtime.
Benefits of Using a 3 Way Manifold Valve
Employing 3 way manifold valves in industrial systems comes with numerous benefits:
- Increased Efficiency: Streamlines processes by allowing multiple pathways for fluid flow without requiring multiple separate valves.
- Space-Saving Design: Reduces the need for extensive piping and additional fittings, leading to a more compact system.
- Improved Control: Offers enhanced control over system processes, allowing for better management of fluid properties and conditions.
- Cost-Effective: By minimizing the need for additional components and optimizing flow management, these valves can lead to significant cost savings over time.
How to Install and Maintain 3 Way Manifold Valves
Installing a 3 way manifold valve correctly is essential for its performance and longevity. Follow these steps:
Installation Steps
- Preparation: Ensure the work area is clean and free of any debris or contaminants.
- Shut Down the System: Before installation, turn off all power sources and fluid supplies.
- Install the Valve: Align the valve with the piping and fasten it securely using the appropriate fittings and tools.
- Check for Leaks: After installation, gradually turn on the fluid supply and check for any leaks around the valve joints.
Maintenance Practices
Regular maintenance keeps 3 way manifold valves in peak condition. Consider implementing the following practices:
- Routine Inspection: Regularly check for signs of wear, corrosion, or any fluid leaks.
- Lubrication: Ensure moving parts are lubricated according to manufacturer specifications to avoid wear.
- Replacement of Seals: Regularly replace seals and gaskets to maintain integrity and prevent leaks.
Conclusion
In summary, the 3 way manifold valve is a vital component for regulating fluid flow across various industrial applications. Its ability to control flow direction effectively and efficiently makes it indispensable in sectors such as oil and gas, chemical processing, and water treatment. By understanding the types, applications, and best practices associated with these valves, businesses can significantly enhance their operational efficiency and safety. Invest in quality 3 way manifold valves to ensure peak performance and reliability in your fluid management systems.
For Quality Valves, Visit TechTubes.in
If you're looking for high-quality 3 way manifold valves and other related products, don't hesitate to visit TechTubes.in. Their extensive range of tube fittings, ferrule fittings, forged pipe fittings, and manifold valves are designed to meet the rigorous demands of modern industrial applications.